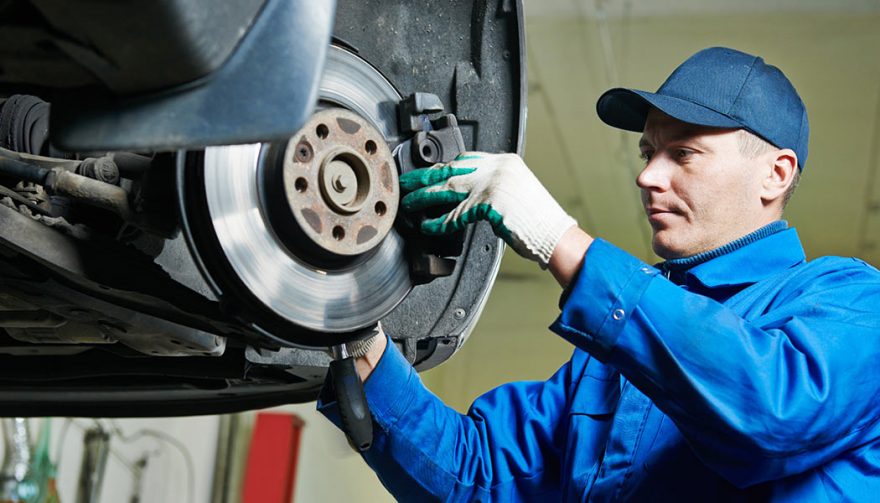
Before working with your new disc pads, place a layer of masking tape over their friction surfaces to keep them free of greasy fingerprints.
Brake Repair Secrets – Tips From A Pro
Ever have a brake problem? Working on your car’s brakes is a rite of passage. Brakes wear out faster than any other parts on your vehicle, so it’s one of the first repairs you do yourself. Besides, they look deceptively simple to work on, and you can get tons of free advice from well-meaning friends, neighbors, and from the friendly people at your parts store.
Yet despite all that you can easily end up with brake noise, steering wheel shimmies, and that most common complaint, a brake pedal that feels ‘mushy’ or that sinks too close to the floor. Why all the problems, even if you followed the instructions in a repair manual?
Because it’s just like following a recipe in a cook book. The food never looks as nice as it does in the book’s pictures, and never really tastes as good as you imagined it would. That’s because the cookbook assumes that you know a lot of little secrets they don’t explain, like how to mix things properly, and other weird stuff. And as married men know, women safeguard that critical knowledge through some unspoken code of secrecy.
So to help you avoid some common brake troubles, here are some tips I learned over the years as a technician and repair shop owner.
Give Your Brake Fluid A Little Respect
Brake fluid is hygroscopic. That means it has no water content, because it needs to have a very high boiling point to withstand the intense heat of braking. But its ‘dryness’ makes it absorb moisture from the atmosphere, even in a so-called sealed system. That tiny bit of absorbed moisture will cause corrosion to form. Gravity then pulls the corrosion to the lowest points in the system, the disc calipers. If you’ve ever removed a caliper piston you’ve probably seen that corrosion, perhaps lots of it if the vehicle had been driven through deep water.
The common advice you might get is to simply use a big C-Clamp to push the caliper pistons back into their bores, to allow room for your new disc pads. But doing that will also push all that corrosion back through the brake lines and into the master cylinder. Not good, because the master cylinder has tiny flat washer valves that must remain surgically clean to seal against each under braking pressure.
The danger might not be apparent at first. Under normal to hard braking the fluid’s pressure will force the valves tightly closed, and they will operate normally. But under very light pressure, like when creeping slowly through traffic and ‘feathering’ the brake pedal, the dirty valves can suddenly bypass, release all pressure, and make the pedal sink rapidly to the floor. That really wakes you up fast.
So before you compress the caliper piston with your C-Clamp, open the bleeder valve to let the fluid escape. Simple. You might see that the bleeder valve is clogged with corrosion, so first remove it and clean it out.
Don’t Damage Your Brake Hoses
If you have to remove a disc caliper, don’t use Vise-Grips to clamp the flexible hose shut to prevent fluid loss. That can permanently crimp the semi-soft hose, which will then restrict the flow of fluid and cause a brake pull to the opposite side when stopping. Even worse, crimping the hose tightly shut could cause a tiny tear in the inner wall of the hose. Brake fluid under pressure will push past that tear, and cause a very visible bubble in the outer lining of the hose. Eventually the hose will burst.
Instead, close off the open hose with plastic sandwich bags. You will find those in your kitchen, that room in your house where you also find the cold beer. Just wrap the bag around the open hose end, double it of you like, and tie it all up snugly with a rubber band. Those are free, too. They come on junk mail.
Prevent Noises Before They Happen
Perhaps your brakes make random popping noises. Usually it will happen at slow speeds, like when backing out of your driveway and braking in reverse. It can be rather loud and unsettling, too, as if someone had hit your car’s chassis with a sledgehammer. That noise happens when the slightly moving caliper slides are dry, binding up and then breaking loose. Bang!
Preventing that noise takes an easy, but often overlooked, procedure. It’s just like that recipe book that leaves out key information that you need to know. So always clean the caliper slides, pins and the contact surfaces that allow movement for the caliper to re-position itself, ever so slightly, as it compresses when you brake, then retracts when you release the pedal.
To clean it all, use the collection of wire brushes you got from Harbor Freight. Sandpaper the really rough parts. Then apply high-temperature brake caliper grease to all moving contact surfaces before reassembly. The new hi-temp brake grease will have a copper color.
It Sounds Like A Broken Record
Perhaps your brakes started making a click-click-click noise after you had them resurfaced. The higher the speed you brake from, the faster the clicking occurs. That noise happens because the rotors were not finished smoothly enough, and were left with tiny machine grooves on them that resemble the tracks on old phonograph records (those came before 8-track tapes, cassettes and CDs).
Under braking, those tiny grooves will pull the disc pads and calipers outward till they can’t move any further. When the caliper pops back into position it makes the clicking noise. As you keep braking, the broken record keeps playing. To fix that, the rotors will have to be machined properly, to a very smooth surface finish. The hard cast iron rotors will not simply ‘wear themselves into condition’ with use. Besides, if the rotors were machined that poorly, your car probably also has a steering wheel shimmy when you apply the brakes.
My New Brakes Squeal
In addition to being very smooth, the rotor surfaces have to be clean of all microscopic machining dust. During the machining process, the lathe’s cutting bit will ever so slightly magnetize the surface of a cast iron brake rotor. It’s just like rubbing a screwdriver tip against iron to magnetize it. The rotor will attract and hold tiny iron dust. Then the dust imbeds itself into your new brake pads, causing the squealing noise.
Cleaning your resurfaced rotors with brake cleaner will not remove cast iron dust. Only soap and water will remove it, and there might be so much fine dust washing off that you will be amazed. Dishwashing liquid and a sponge works great. Get them from that same room where you find the cold beer. Dry the rotors with a rag dipped lightly in lacquer thinner. It evaporates quickly, and leaves no trace film.
Brake Pedal Feel Mushy?
Bleeding brakes is another rite of passage. I don’t like those vacuum type bleeders. Inducing a vacuum in a brake system can cause air to be drawn in passed the caliper piston’s lip seals. Lip seals can hold tremendous fluid pressure in…the harder you brake the better they seal. But they are one-way seals, and are lousy at keeping air out when a vacuum is induced.
If you don’t have access to a professional brake ‘pressure bleeder’ this tip might work. If you open one caliper bleeder a few turns, your system will (often) gravity bleed itself. Be sure to keep the master cylinder full at all times. This also gives you the advantage of flushing out all the old fluid. Bleed one caliper as you reassemble another one. Be patient.
Keep It Clean
Before working with your new disc pads, place a layer of ordinary masking tape over their friction surfaces to keep them free of greasy fingerprints. Remove the tape just before bolting the caliper into place. If you do get grease on the pads, don’t worry. But don’t use any liquid, like brake cleaner, to get it off. Liquid cleaners will only soak into the friction material. Instead use 80 grit sandpaper to lightly buff off the grease. Clean any fingerprints off the installed rotors with the rag you dipped in lacquer thinner.
Final Words
Put a dab of anti-seize compound on the outermost few threads of the wheel studs before you put the wheels back on. That will greatly reduce the chances of a cross-threaded lug nut.
Finally, break in your new disc pads properly. Accelerate to 10 mph, then stop normally. Again to 20 mph, and stop. To 30, stop, then to 40, stopping normally. Then drive for two minutes to cool off the rotors. They need the moving air to cool down. Then repeat the normal braking a few more times. You don’t want to overheat the new pads by braking too hard, as that will produce ‘baking heat’ that will glaze your new disc pads. Then the squeal will never stop.
In the next part, we’ll cover drum brake and parking brake issues. If you have an older car, or if you are doing a resto-mod, you’ll get some good info from it. Drive safely!